我国天然气中的氦气含量相较于国际水平偏低,这直接导致了我国氦气的自然储量较为有限。鉴于这一现状,我国在从天然气中提取氦气的工艺设计上,必须更加注重流程的优化,力求实现简化、节能、环保以及高效的目标。简而言之,我们需要开发出一套既经济又环保的提氦技术,以最大化利用有限的氦气资源。
由于国内在提氦领域的流程相对滞后,且设备构成复杂,导致了提取氦气的成本居高不下。这一状况自1996年起持续了相当长的一段时间,使得我国不得不依赖大量进口来满足对氦气的需求。为了应对这一挑战,我国开始积极探索如何简化提氦设备、降低生产成本,并积极引进先进的科技技术,以期在提氦领域实现自给自足并提升国际竞争力。
国内众多专家对氦气的提取与精制技术进行了深入细致的研究。其中,章炎生等学者特别关注了合成氨制备过程中产生的驰放气,这一副产物中不仅富含氢气、氮气,还包含了氦、氩、氖、氙等宝贵的稀有气体。他们指出,通过对驰放气进行进一步的加工处理,并辅以其他技术手段,可以有效地从中提取出氦气,实现资源的最大化利用。
四川化工厂在合成氨尾气提氦工艺方面进行了更为深入的探索。他们发现,合成氨尾气中氦气的浓度可达到0.5%~2%,这一浓度水平使得尾气中的氦气具有极高的提取价值。为了高效提取这些氦气,四川化工厂介绍了多种方法,包括吸附法等,这些方法的应用有望显著提升我国氦气的自给能力,减少对进口氦气的依赖。
上世纪九十年代,四川化工研究所与四川威远气田携手合作,共同探索了膜分离技术在提氦方面的应用潜力。他们选用了聚碳酸脂膜进行试验,通过二级分离工艺,成功将氦气浓度提升至90%,同时氦气回收率也高达90%。然而,聚碳酸脂膜的使用寿命短暂且成本高昂,这一技术面临显著的经济挑战。随后,在1994年和1995年,疏朝龙和陈华等学者分别深化了膜分离技术的研究,前者因实际条件限制仅停留在编程模拟阶段,而后者则尝试将膜分离与深冷工艺相结合,通过模拟计算发现聚矾复合膜对氦气/甲烷的选择性超过100,展现出工业化应用的潜力。
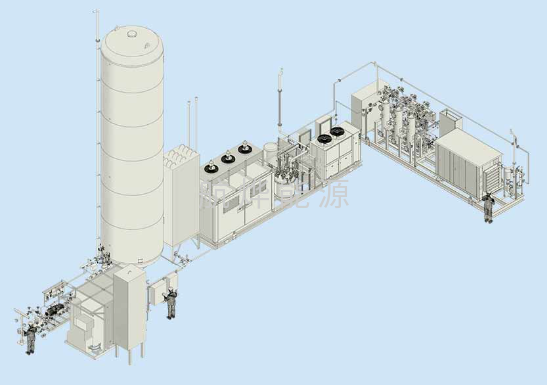
近年来,膜分离提氦技术取得了显著进展,特别是聚酞亚胺膜因其高选择性和高透量特性,成为具有工业化价值的新选择。
与此同时,深冷法作为另一种广泛研究的提氦技术,也在我国有着悠久的历史。四川威远天然气气田早在十九世纪六十年代就引入了深冷法提氦装置,但由于经济因素和产能下降等问题,该装置在1966年被迫停产。深冷法流程复杂且能耗巨大,设备投资费用高昂,尽管后来引入了膨胀机制冷技术以降低能耗,但整体成本仍高于进口氦气。
在低温提氦流程方面,我国最初采用的是焦耳-汤姆逊节流循环制冷技术,随后逐步引入膨胀机制冷流程以简化流程并节省能耗。然而,即便采用膨胀机制冷,提氦流程的成本依然高于直接购买进口氦气,这促使我国继续探索更加高效、经济的提氦技术。
早期的深冷法提氦工艺主要依赖于氨预冷的单塔分离装置,该装置通过常压液甲烷冷凝段和减压液甲烷冷凝段进行精馏,并采用绕管式换热器进行低温换热。然而,随着气田开采时间的延长,原料气的压力逐渐下降,迫使设备增设压缩机以维持流程顺畅,从而显著增加了投资和运营成本。
为了应对原料气压力和组成变化带来的挑战,我国创新性地提出了前膨胀提氦工艺和后膨胀提氦工艺这两种双塔分离流程。这两种工艺均引入了膨胀机和高压单循环制冷单元,并将预冷方式从氨预冷升级为丙烷预冷,同时更换了部分高效设备,如采用板翅式换热器以降低能耗和成本。
前膨胀提氦工艺的特点是先进行膨胀操作,导致流程的操作压力和温度均较低,这对塔材质提出了更高要求,且膨胀机的操作弹性较低,影响了装置的适应性。相比之下,后膨胀提氦工艺则通过后膨胀技术有效提升了粗氦浓度,操作温度和压力均较高,降低了对塔材质的要求,并提高了装置的适应性。
此外,当前还有学者在探索深冷法与膜分离法的耦合应用。例如,张良聪等人利用丙烷预冷的混合冷剂制冷技术,将天然气冷却液化后,再通过HYSYS模拟优化深冷膜联合提氦工艺。这一创新工艺结合了深冷法和膜分离法的优势,经过液化流程与两级膜过程后,氦气的回收率可高达96%,展现了巨大的应用潜力和经济效益。
天然气提氦的主要技术手段包括低温冷凝法、膜分离法、吸附法、吸收法、扩散法以及水合物法等。
低温冷凝法因其高效性而在全球范围内得到广泛应用。我国自十九世纪起便引入了该技术,并在四川威远天然气田建立了相应的天然气液化提氦装置。然而,标准的低温冷凝法难以完全液化天然气中的氮气、氢气等成分,因此该工艺通常分为三个关键步骤来优化操作效果:
在含氦天然气的预处理与净化阶段,由于不同地区的天然气成分各异,其中含有的硫、二氧化碳、水等杂质可能会干扰低温装置的正常运行,甚至导致水合物堵塞管道或腐蚀设备。因此,在进行低温处理之前,必须对天然气进行预处理,以达到低温操作所需的纯净度标准。
针对天然气中的酸性气体(如硫化氢和二氧化碳),常用的脱除方法包括化学溶剂吸收法、物理溶剂吸收法、物理化学吸收法、直接氧化法、干法脱硫以及膜分离法等。鉴于提氦工艺对天然气中酸性气体含量的严格要求(通常要求硫化氢含量低于4ppm,二氧化碳含量低于一定标准),需根据具体情况选择合适的脱酸流程,以确保后续提氦过程的顺利进行。
在粗氦提取阶段,通过采用特定的制冷技术,天然气被部分液化并经历两次提氦塔的处理过程,最终能够高效提取出粗氦,回收率可达到95%以上。这一过程的关键在于利用不同组分液化点的差异,使得氦气作为几乎不液化的成分被有效分离出来。经过两次冷凝后,获得的粗氦浓度通常介于60%至70%之间。
随后进入氦气精制阶段,由于天然气中除了氦气外还可能含有氢气等难以液化的气体,这些气体在精制前需要被去除。工业上常采用催化氧化法来有效脱除多余的氢气。处理后的粗氦再经过高压冷凝吸附过程,进一步去除其他杂质,最终可将氦气的纯度提升至99%以上。
另一方面,膜分离法作为一种重要的提氦技术,其研究始于1965年,由Stem等人率先开展。膜分离法利用分离膜两侧的压力差导致不同组分间传递速率的差异,从而实现气体的有效分离。这种方法具有操作简便、能耗较低等优势,在氦气提取领域展现出广阔的应用前景。